Restart Center: a new offer is taking shape
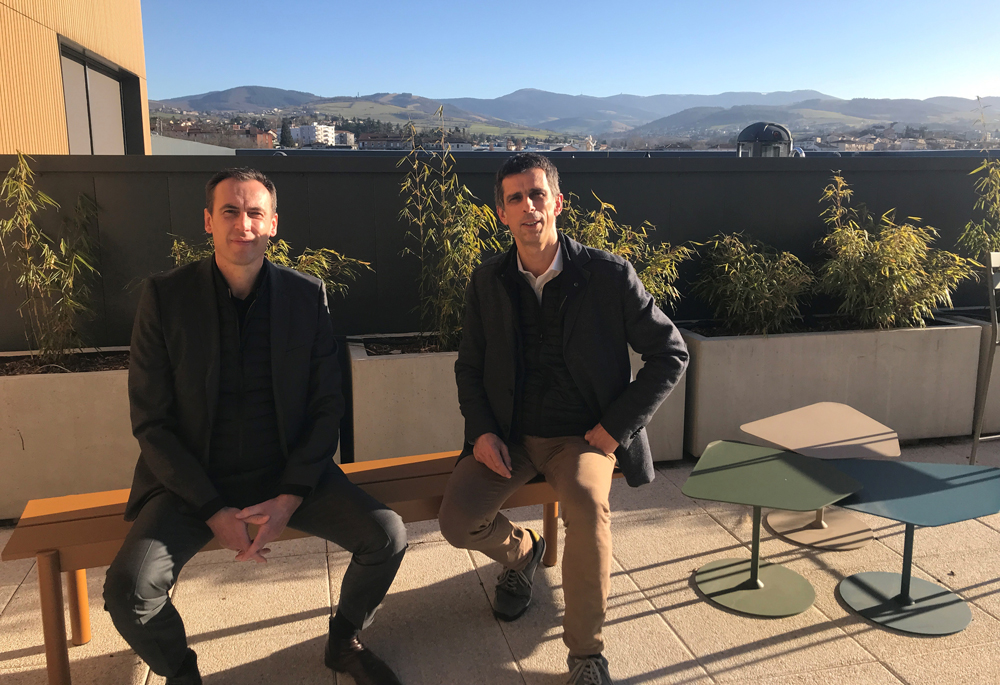
The first center to refurbish used Haulotte equipment will shortly be opening its doors at the L’Horme site in France. This is a new activity for the Group, its customers and the operators who will be trained to develop new skills. The latter discovered the new opportunities opening up to them on January 4.
Ultimately, the Restart Center will enable Haulotte to propose a Manufacturer offer on the used equipment market.
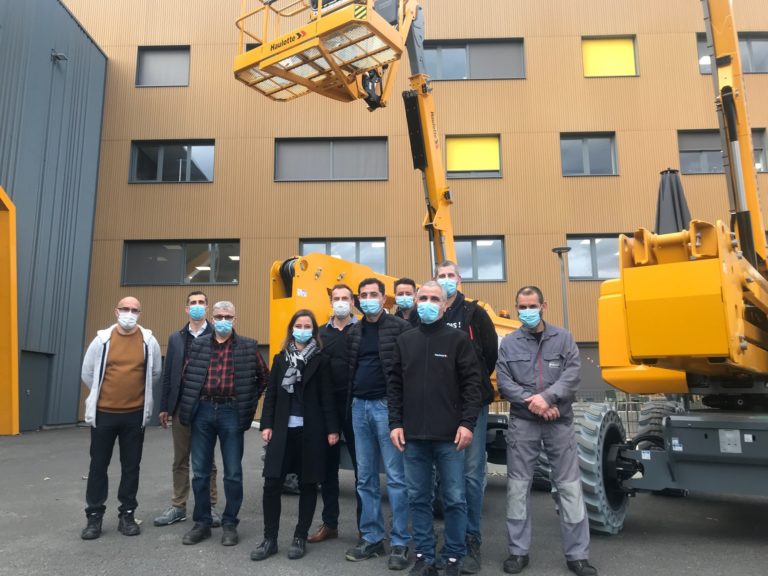
The refurbishment offer, which is still in the middle of being launched, is part of the Group’s global strategy. This includes the used equipment market as one of its strategic pillars.
Refurbishment increases the service life of machines and provides solutions to current major issues such as reducing the cost of ownership or Corporate Social Responsibility (CSR).
The offer will initially be limited to the European area to better manage compliance with the standards. Moreover, the European market is very active and has a large number of subsidiaries. The machine fleet is very large there, and this represents an opportunity for the used equipment market.
Second Life, Used Equipment Refurbishment: two separate offers
For several years now, the Group has been providing its customers with an offer called “Second Life”. This offer consists in refurbishing machines in our customer’s fleets, with three offers:
- Replacement of visible parts (labels, wheels, paint) to give equipment a real “face-lift” to increase its rental value.
- Repair and replacement of major mechanical parts to ensure the equipment safe to use and to optimize the total cost of ownership.
- Lastly, the addition of new functions or technologies to increase the performance of the machines in the fleets.
The used equipment refurbishment offer concerns machines which have been bought back by Haulotte when customers renew their fleets. The “Used equipment” activity started in 2018. Up till now, it focused on the resale of these machines in the same condition as received. With the Restart Center, the Group will be able to sell machines that have been repaired and restored to “ex works” compliance. This Manufacturer offer will bring real added value to the machines and enable customers to quickly constitute or expand a fleet with reduced investment costs.
Lengthy preparations
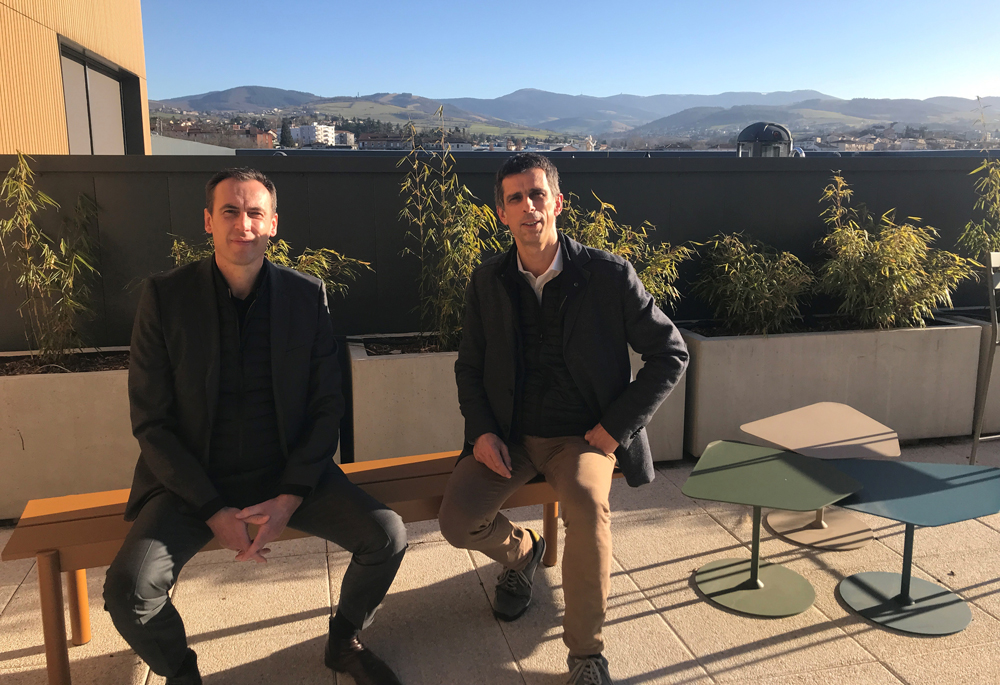
It is the job of Emmanuel Chabaneix and Ludovic Jankov to set up the Restart Center. They both share a strong customer culture, forged as Customer Service Manager for the subsidiaries in the Americas zone for Emmanuel Chabaneix, and as Used Equipment Manager to support all the subsidiaries for Ludovic Jankov.
“We worked on the business plan together from last summer up until the end of the year. Our priority is first to train operators and constitute our stock of platforms. Sales will come later,” they specified.
The teams at the site discovered the training program at the start of January, during an integration day. Given the wide range of machines to be refurbished, this program will last at least for the whole of 2022 and will evolve according to the models to be repaired.
The Restart Center offer will be organized on three levels:
- Verified: machines (up to 15 years). Restored to compliance with the standards.
- Certified: machines (up to 10 years). Optimized refurbishment with a few cosmetic repairs possible. 3-month warranty.
- Certified +: machines up to 6 years old. Full technical and cosmetic refurbishment. 6-month warranty.
A promising sector
“Used equipment is a very large market segment in general, particularly given the current circumstances. For customers, this means two things: immediate availability of the machines and less investment,” explain Emmanuel and Ludovic.
The diversification of our offer towards the used equipment market is therefore a strategic focus for development. It will enable the Group to reach new customers and to offer new supplementary services such as warranty extension or the maintenance/repair/spare parts department, not to mention ad hoc finance offers. Finally, it will be possible to set up certain options on the machines, for example with regard to safety, without affecting the initial approval.
This is a new avenue to respond to the economic and environmental requirements of our ecosystem!
Further reading
Strategic Projects: stay tuned!
David Alviani, PMO (Project Management Officer) of the Group gives us an update on the current situation.
continue readingImprovement of safety awareness in Haulotte Shanghai
In the last week of January, Haulotte Shanghai held the 2020 Annual meeting at the Shanghai office.
continue reading